Ceramic-rubber composite liner in chemical equipment: wear-resistant and anti-corrosion advantage analysis
Date: 2025/07/07 Categories: Company News Views: 428
Excerpt:
Ceramic rubber composite liner is a kind of wear-resistant and corrosion-resistant material widely used in chemical industry, which combines the high hardness of ceramic and high elasticity of rubber, and is suitable for the protection of the equipment under the harsh working conditions. The following is its detailed introduction in the chemical industry
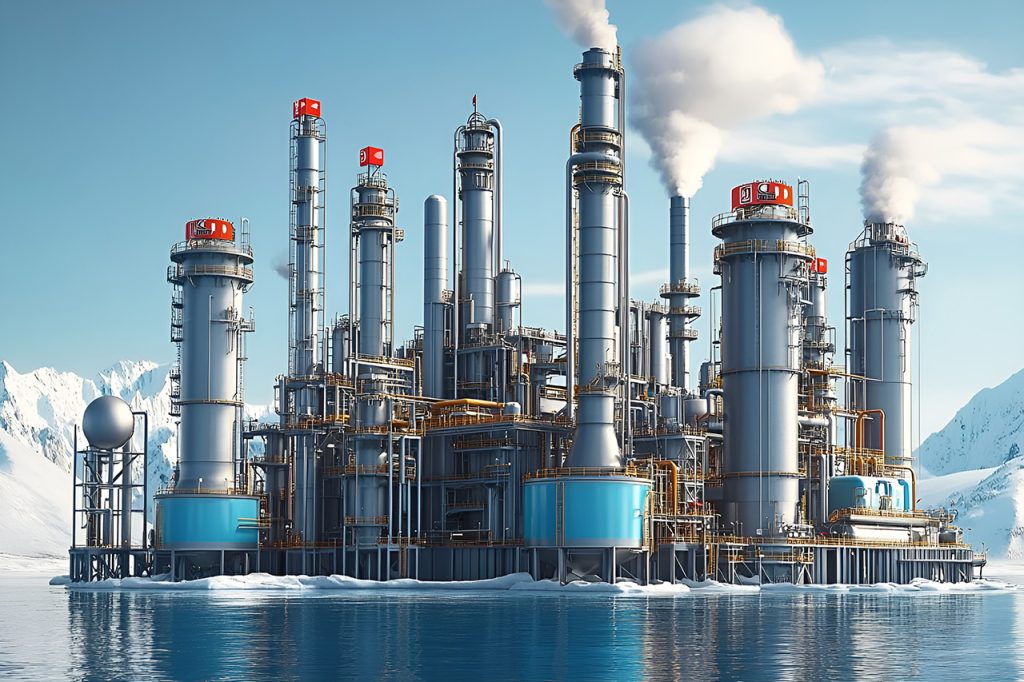
Ceramic Rubber Composite LinerIt is a widely usedmetallurgyThe industry's wear-resistant and corrosion-resistant materials, combining the high hardness of ceramics and the high elasticity of rubber, are suitable for the protection of equipment under harsh working conditions. The following is a detailed description of its use in the chemical industry:
1. Material structure and characteristics
- ceramic layer: High hardness ceramics such as alumina (Al₂O₃) or silicon carbide (SiC) are commonly used to provide excellent resistance to wear, chemicals, and high temperatures (some ceramics can withstand more than 1000°C).
- rubber layer: Commonly used natural rubber or synthetic rubber (such as styrene-butadiene rubber, neoprene rubber), giving the material impact resistance, shock absorption, sealing and flexibility, as well as resistance to acid and alkali corrosion.
- composite process: The ceramic is tightly bonded to the rubber through high temperature vulcanization or adhesive technology to form a rigid-flexible composite material.
2. Application scenarios in the chemical industry
- Pipe and chute lining: Used for lining pipes conveying abrasive slurries (e.g. mineral slurries, acid and alkali solutions) to reduce wear and clogging.
- Reactor/tank lining: Protects equipment from chemical media corrosion and material washout, extending service life.
- Centrifuges and separation equipment: Resistant to wear and tear caused by high speed rotation during solid-liquid separation.
- Flue & Dedusting Systems: Resistant to corrosive gases (e.g. SO₂, HCl) and particulate matter.
3. Core strengths
- abrasion resistance: Ceramic hardness (HRA≥85) far exceeds that of steel and is suitable for handling media containing hard particles.
- corrosion resistance: The rubber layer is resistant to acid and alkali corrosion, and the ceramic layer is stable against oxidizing media.
- impact resistance: Rubberized substrate absorbs vibrations and shocks and avoids brittle cracking of ceramics.
- lightweighting: than pure metallinerLight 30%~50% to reduce equipment load.
- Convenient installation: Can be made into modular liners, fixed by bolting or bonding, easy maintenance and replacement.
4. Comparison with other liners
Liner type | vantage | drawbacks |
---|---|---|
Pure ceramic liners | Ultra-high wear resistance | Highly brittle and easily broken |
Pure rubber liner | Good impact resistance and low cost | Insufficient abrasion resistance |
Metal (e.g. stainless steel) liners | high strength | Poor corrosion resistance and high weight |
Ceramic Rubber Composite Liner | Excellent overall performance | Higher cost (but long life and good value for money) |
5. Selection and considerations
- Media Characteristics: Selection of ceramic type according to corrosivity (pH), temperature, particle hardness (e.g. alumina is suitable for neutral/weak acids and bases, silicon carbide is resistant to strong acids).
- working pressure: High-pressure environments require the selection of laminating processes with high bond strength.
- Installation: Flexible liners are required for curved surfaces and rigid liners are available for flat surfaces.
- Maintenance Cycle: Periodically check for dislodged ceramic blocks or deteriorated rubber.
6. Market and development trends
- technological innovation: The application of nano-ceramic coatings and high-performance synthetic rubbers (e.g., fluoroelastomers) improves the adaptability to extreme operating conditions.
- environmental demand: Heavy metal-free, recyclable materials meet the requirements of the greening of the chemical industry.
- Intelligent monitoring: Some manufacturers integrate wear sensors to enable liner life prediction.
summarize
Ceramic rubber composite liner solves the dual challenges of wear and corrosion faced by chemical industry equipment through material synergy, especially suitable for highly corrosive slurry transportation, reaction equipment protection and other scenarios. Its long life and low maintenance cost can significantly reduce the loss of downtime, is the ideal choice for modern chemical equipment upgrading.